Introduction
Wet mix shotcrete is an essential technique in modern construction, offering a flexible and efficient solution for applying concrete to complex surfaces. Unlike traditional methods, wet mix shotcrete involves the pre-mixing of water with concrete before it is pneumatically sprayed onto surfaces at high velocity. This process ensures a high degree of control over quality, making it particularly suited for projects that require precision, durability, and speed.
Understanding the ins and outs of wet mix shotcrete is crucial for achieving optimal results in a variety of construction applications. Whether you’re working on tunnels, retaining walls, or intricate architectural designs, knowing how this method works and the equipment involved can help ensure successful project outcomes. In this comprehensive overview, we’ll explore what wet mix shotcrete is, its application process, the necessary equipment, and its many advantages over traditional methods.
TABLE OF CONTENTS
1. What is Wet Mix Shotcrete?
Wet mix concrete is basically a method of making and pouring concrete into hard to reach places. The wet mix concrete is basically mixed with water before being poured through a high velocity nozzle onto a surface. This unique process requires the use of specially designed nozzles to direct the concrete where it is needed, providing a strong, dense and durable application.
The term “wet mix” means a liquid seeming mixture. Differing from dry mix shotcrete, where water is introduced only at the tip of the nozzle during the spraying process. In wet mix shotcrete, the concrete is already mixed with water before the application process. Providing better control of the spraying and accuracy, which proves important in construction projects that require high precision and accuracy.
Wet mix shotcrete is mainly used in newly designed construction processes and reparation work, it is most commonly used in areas that require the application of concrete onto irregular surfaces. This unique method gives strong adhesion and strength to the we mixture, making it a go to choice for construction in difficult environments such as tunnels, pools, dams and walls.
2. Understanding the Wet Mix Shotcrete Process
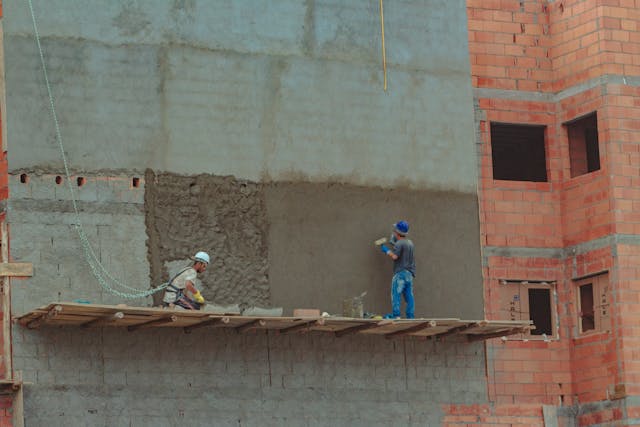
The wet mixture of the shotcrete process is made by the initial preparation of concrete mix. The wet mix is first made by mixing water, cement, aggregate and other required mixtures together to make a homogenous mixture. Once added together, the wet concrete is then sent through a nozzle using high pressurized pumps and is sprayed onto the desired surface.
As the concrete mixture is sent through the nozzle at a high velocity, ensuring proper adhesion and hardening upon impact. This velocity is key to the durability and dense structure of the applied mixture. Wet mix shotcrete is usually applied in layers, providing better control over the thickness and density of the mixture to provide better hardening over the preferred surface. This ultimately allows for reducing the risk of cracking during the hardening process. Unlike the dry version of mix shotcrete, which usually requires the nozzle for water control, wet mix concrete ensures consistency in the application process, reducing the chances of errors and providing consistent layering of concrete.
The most unique feature of wet mix shotcrete is the fact that it can be applied both manually and through automatic sprayers, which can improve the rate of accuracy and reduce labor costs. Robotic spray features are useful for large-scale construction projects, providing consistent spraying over large areas.
3. Equipment Used for Wet Mix Shotcrete
The success of a wet mix shotcrete application largely depends on the quality of the equipment used. Three key pieces of equipment play a central role in this process: concrete pumps, nozzles, and, in some cases, robotic spray systems.
Concrete Pumps:
Wet mix shotcrete requires high-pressure pumps capable of delivering pre-mixed concrete through long hoses to the nozzle. There are different types of pumps used depending on the project requirements, such as piston pumps and rotary pumps. These pumps must maintain consistent pressure to ensure that the concrete reaches the nozzle with the necessary velocity for proper application.
Nozzles:
The nozzle is critical in controlling the direction, spread, and velocity of the shotcrete. Different types and sizes of nozzles are available, with each type designed to handle various shotcrete compositions and project demands. Some nozzles allow for finer control over spray patterns, while others are built for high-volume applications.
Robotic Spray Equipment:
For larger or more complex applications, robotic systems are often used. These machines are programmed to apply shotcrete uniformly, ensuring precision and consistency across surfaces. Robotic systems are especially valuable for projects like tunnels, domes, and other structures where manual application would be labor-intensive or prone to inconsistencies.
By using the right equipment, contractors can ensure that the wet mix shotcrete is applied evenly and efficiently, leading to better project outcomes.
4. Mix Design and Adjustments
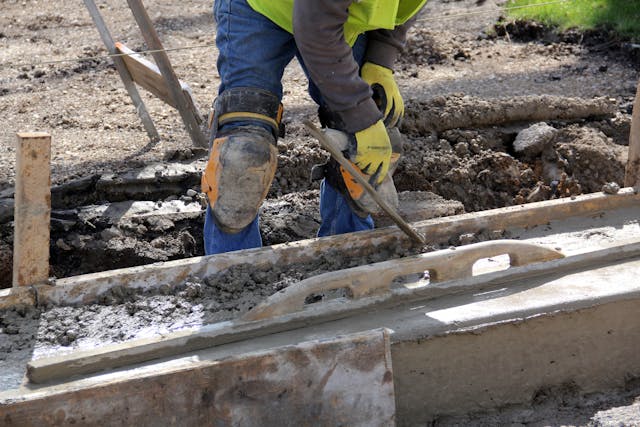
The mix design for wet mix shotcrete is a critical factor that directly influences the strength, durability, and workability of the concrete. Achieving the right mix involves balancing several key components: cement, aggregate, water, and admixtures.
- Cement: The amount of cement used in the mix affects the strength and bonding ability of the shotcrete. A higher cement content can increase the compressive strength but may also lead to cracking if not balanced properly with other ingredients.
- Aggregate: The size and gradation of the aggregate play an important role in the shotcrete’s overall performance. Fine aggregates are often preferred for wet mix shotcrete, as they contribute to smoother application and better bonding on surfaces. However, for certain projects, a more robust mix with larger aggregates may be used to enhance strength.
- Water-Cement Ratio: The water content in the mix must be carefully controlled. Too much water can weaken the concrete, leading to lower strength and increased permeability. Too little water can make the concrete difficult to pump and apply, potentially leading to clogs or poor adhesion.
- Admixtures and Fibers: Various admixtures can be added to the mix to improve specific properties. For example, accelerators can speed up the setting time, making the shotcrete ideal for projects where quick application and hardening are necessary. Fibers, like steel or synthetic fibers, are often used to enhance the shotcrete’s resistance to cracking and improve its structural integrity.
Mix adjustments may be required depending on the specific application and environmental conditions. For example, in hot weather, more water may be needed to keep the mix workable, while in colder conditions, accelerators may be added to speed up curing.
By carefully adjusting the mix design, contractors can tailor the shotcrete to meet the precise needs of their project, ensuring optimal performance and durability.
5. Admixtures and Additives
Admixtures and additives are essential components in wet mix shotcrete, enabling the mix to achieve specific performance characteristics suited for different construction environments. The use of these substances allows contractors to optimize the concrete for a range of conditions, from achieving faster setting times to enhancing structural integrity.
Shotcrete Admixtures:
Admixtures are chemicals added to the shotcrete mix to modify its properties. Common admixtures in wet mix shotcrete include accelerators, retarders, water reducers, and air-entraining agents. Accelerators, for instance, are frequently used in wet mix shotcrete to speed up the setting process, allowing the concrete to harden more quickly in time-sensitive projects, such as tunnel construction or repairs in areas with constant moisture exposure.
Shotcrete Additives:
In addition to admixtures, fibers are commonly used in wet mix shotcrete to reinforce the material. Fibers like steel or synthetic materials improve the tensile strength of the shotcrete, preventing cracks and increasing durability, particularly in structures exposed to heavy loads or extreme weather conditions. Additives such as silica fume can also be incorporated to reduce permeability and enhance the shotcrete’s resistance to aggressive environments like water-retaining structures or chemical exposure.
The correct selection and dosage of admixtures and additives are vital to achieving the desired outcomes in wet mix shotcrete applications. Each project has unique requirements, and using the right combination of these components ensures that the shotcrete performs optimally in its environment.
6. Safety Considerations in Wet Mix Shotcrete
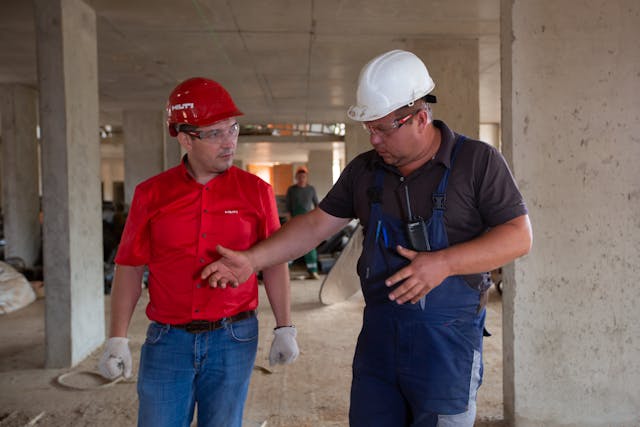
Safety is a paramount concern when working with wet mix shotcrete due to the high pressures involved in its application and the use of heavy machinery. Understanding the risks and implementing safety measures helps to prevent accidents and ensure a secure working environment.
Concrete Pumping Safety:
Wet mix shotcrete is applied using concrete pumps that operate under high pressure. It is crucial to ensure that the pumps are well-maintained and operated by trained personnel to prevent equipment failures or bursts in the line. Proper safety protocols, such as regular inspections of hoses and fittings, are essential to avoid unexpected hazards like blowouts, which can cause serious injuries.
Concrete Line Pressures:
Wet mix shotcrete is applied through hoses at high pressure, and monitoring the line pressure is vital to ensure a smooth and safe application. Over-pressurizing the lines can lead to material blockages or hose ruptures, both of which pose serious risks to workers.
Air Supply Requirements:
In addition to concrete, wet mix shotcrete requires a steady supply of compressed air for optimal application. Ensuring that the air supply is consistent and free of contaminants prevents issues that could lead to improper shotcrete compaction or poor adhesion to the surface.
Personal Protective Equipment (PPE):
Workers handling wet mix shotcrete should always wear appropriate PPE, including hard hats, safety goggles, gloves, and protective clothing. The spraying process involves high-velocity concrete, which can be hazardous if not managed properly. Ensuring that all workers are equipped with the necessary safety gear can reduce the risk of injury.
By following established safety practices, contractors can mitigate the risks associated with wet mix shotcrete, creating a safer environment for everyone involved in the project.
7. Applications of Wet Mix Shotcrete
Wet mix shotcrete is widely used in a variety of construction and repair applications due to its flexibility, strength, and ability to adhere to complex surfaces. Its high versatility makes it suitable for both large-scale infrastructure projects and smaller architectural works.
Tunnels and Underground Construction:
Wet mix shotcrete is a popular choice for tunnel linings and underground construction projects due to its ability to adhere to uneven surfaces and provide structural support quickly. Its fast application process allows workers to stabilize walls and ceilings in a shorter amount of time, which is critical in environments prone to collapsing.
Retaining Walls and Dams:
Wet mix shotcrete is commonly used for constructing and reinforcing retaining walls and dams. Its ability to form a durable, water-resistant layer makes it ideal for these applications. Wet mix shotcrete is also effective in repair projects, where it can be used to restore eroded or damaged sections of concrete infrastructure.
Architectural Landscaping:
Wet mix shotcrete is increasingly being used in architectural landscaping projects, where it can be applied to create custom shapes and designs. Its ability to adhere to vertical and overhead surfaces makes it possible to create intricate rockscapes, sculptures, and other artistic structures.
Pools and Water-Containment Structures:
The watertight properties of wet mix shotcrete make it perfect for constructing pools, fountains, and other water-retaining structures. Its ability to form complex, curved surfaces allows for greater design flexibility in pool construction, while its high durability ensures a long-lasting finish.
Whether in large-scale industrial projects or intricate architectural designs, wet mix shotcrete offers a reliable and efficient solution for a wide range of applications.
8. Advantages of Wet Mix Shotcrete
Wet mix shotcrete provides numerous advantages over traditional concrete application methods, making it a preferred choice in many construction projects. Some of the key benefits include:
- High Quality and Durability: Because the concrete is pre-mixed before being sprayed, wet mix shotcrete allows for greater consistency in its composition. This results in a more uniform and dense application, providing better overall durability and resistance to environmental factors.
- Fast Application: One of the most significant advantages of wet mix shotcrete is the speed at which it can be applied. Since the concrete is mixed and ready before being pumped, the process is more efficient compared to dry mix shotcrete, which requires water to be added during the spraying process. This makes wet mix shotcrete ideal for time-sensitive projects.
- Versatility in Application: Wet mix shotcrete can be applied to a variety of surfaces, including vertical and overhead areas, where traditional concrete would be difficult to use. Its flexibility also makes it suitable for complex shapes and designs, offering more creative freedom in construction and architectural projects.
- Improved Control Over Mix Design: Wet mix shotcrete allows for greater control over the water-cement ratio, ensuring that the desired strength and consistency are achieved. This also reduces the risk of errors during application, as the mix is pre-determined before it reaches the nozzle.
- Reduced Rebound Waste: In wet mix shotcrete, the amount of material rebounding from the surface during application is lower compared to dry mix methods. This results in less waste, reducing material costs and minimizing cleanup after application.
Overall, wet mix shotcrete offers superior performance in terms of strength, durability, and ease of application, making it a favored technique in the construction industry.
Conclusion
Wet mix shotcrete has established itself as a versatile and powerful tool in modern construction, offering unique benefits in terms of efficiency, strength, and adaptability. Its ability to be applied to complex shapes, vertical surfaces, and challenging environments makes it an ideal solution for a wide range of projects, from tunnel construction to architectural detailing.
By understanding the wet mix shotcrete process, the importance of mix design, and the equipment involved, contractors and engineers can achieve high-quality, durable results while saving time and reducing costs. Whether used for repair work, new construction, or creative architectural projects, wet mix shotcrete continues to revolutionize the way concrete is applied.
As with any construction technique, proper planning, safety considerations, and the right equipment are key to success. As you explore the possibilities of wet mix shotcrete, consulting with experienced professionals will ensure that your project benefits from the full potential of this innovative method.
FAQs
1. What are the benefits of using wet mix shotcrete over dry mix shotcrete?
Wet mix shotcrete is often preferred for larger projects because the concrete is mixed beforehand, ensuring a consistent quality. It also produces less dust during application and has better control over water content, making it more suitable for high-strength requirements.
2. What type of equipment is essential for wet mix shotcrete?
The key equipment for wet mix shotcrete includes high-performance concrete pumps, specialized nozzles, and, in some cases, robotic spray systems. These help deliver the material at high velocity to ensure it adheres to the surface with proper compaction and strength.
3. Can wet mix shotcrete be used for underwater applications?
Yes, wet mix shotcrete is often used in underwater or water-retaining structures such as dams and swimming pools. Its ability to be applied quickly and adhere strongly to surfaces makes it suitable for environments where water exposure is high.
4. How long does it take for wet mix shotcrete to cure?
Wet mix shotcrete typically has an initial set time of a few hours, but full curing can take up to several days, depending on factors like temperature, humidity, and the type of admixtures used. The curing process can be sped up or slowed down with additives, depending on project requirements.
5. What are the common admixtures used in wet mix shotcrete?
Common admixtures include accelerators to speed up curing, plasticizers to improve workability, and water reducers for achieving a higher strength mix. Fiber reinforcement is also frequently added to enhance durability and crack resistance.